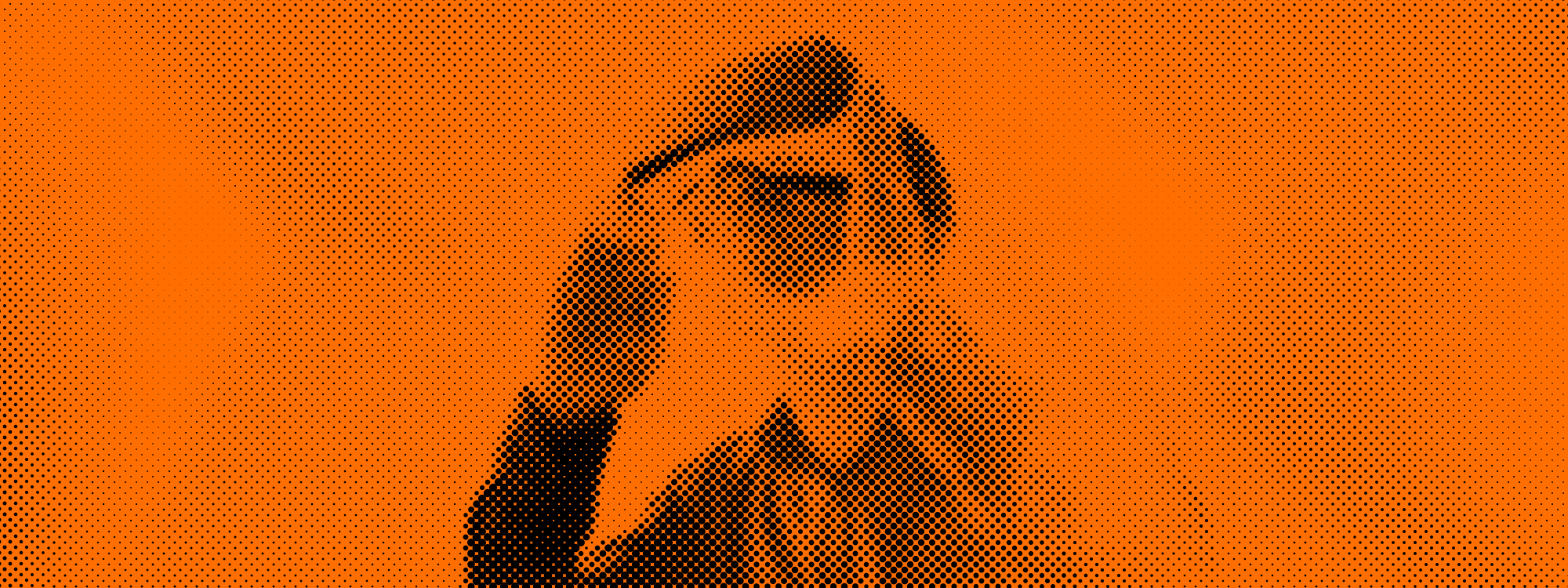
enthusiasticcustomers
would you like to get an insight into our work? our references are what motivates us. please find here descriptions and pictures of our reference projects.
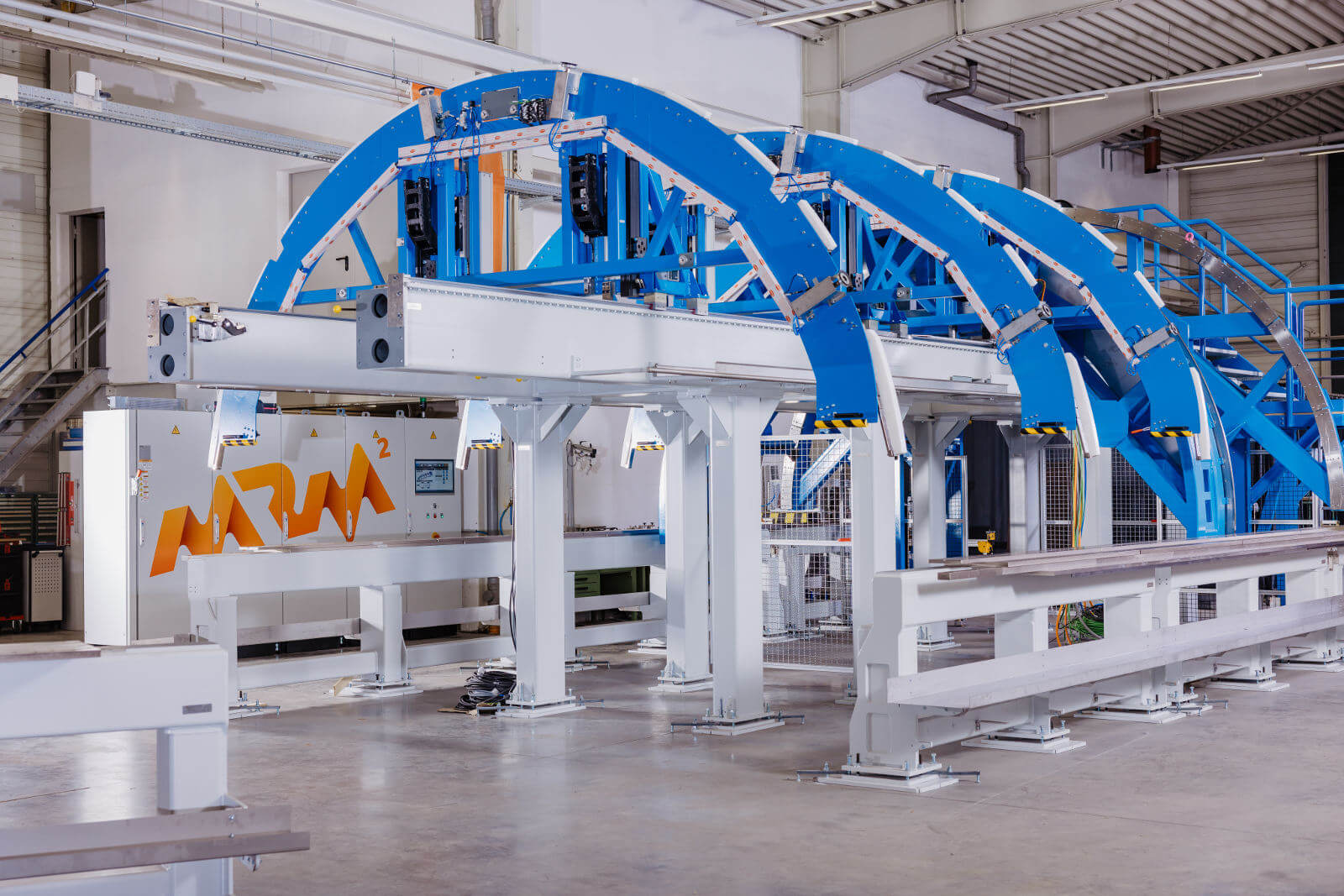
beyond gravity ag
the swiss company beyond gravity ag is a supplier of space products and the world’s leading supplier of composite technology payload fairings and structures for launcher vehicles. new production sites have been established in emmen (ch) and decatur (usa). ariane 5, ariane 6 short and long and vega payload fairings are produced there.
most of the production plants in switzerland and two plants in decatur are equipped with electrical engineering from mrm². at the emmen production site there is a laying table for fibre mats, two plants for equipping fairing half-shells and a highly complex, fully automated plant for processing the fairing half-shells, the horizontal integration station. 17 synchronously running axes, repetitive accuracies of 0.02mm over a length of 26m, tool changing systems including program management, further synchronously running and externally monitored drive systems, multi-user operable visualizations and highly networked different systems. all systems are developed and programmed on the codesys software platform.
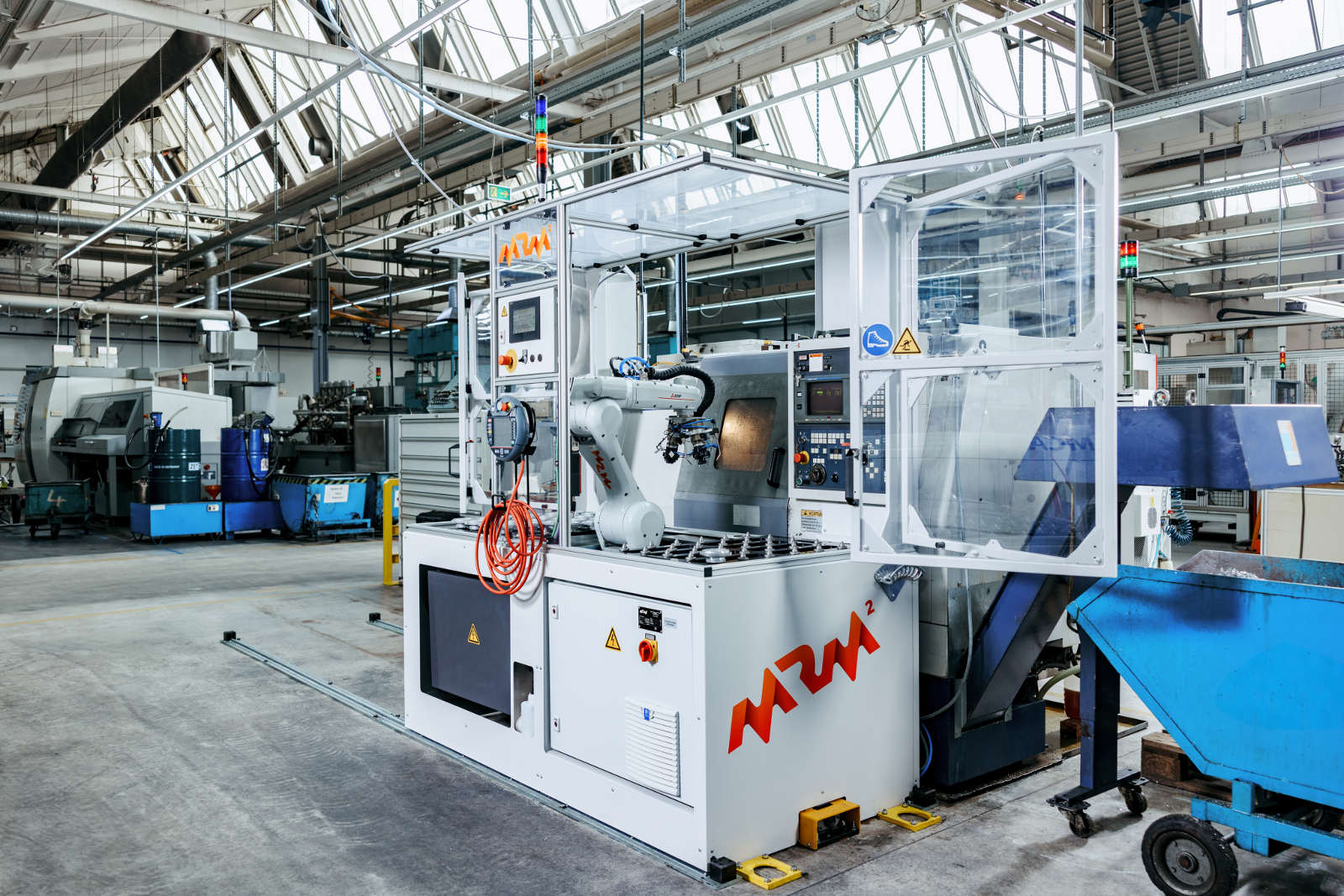
metabowerke gmbh
the company metabowerke gmbh from nürtingen manufactures power tools for professional use. for a lathe that machines pre-cast housing parts for power tools, mrm² designed a robot cell that automates the loading of the lathe, which previously had to be loaded manually. the challenge was to make this loading system communicate with the very old lathe.
the robot picks up a component, opens the sliding door of the lathe, positions it in the chuck of the machine and then closes the sliding door. after the machining process, the robot opens the door again, picks up the part and replaces it with another part to be machined. a total of 30 parts are machined in this way before the cell has to be loaded with new material after 40 minutes. this 40-minute cycle had to be coordinated with a total of 3 machines so that one employee can operate several machines together without losing time. "mrm² implemented our requirement to connect the automated loading to the existing system very well," says hans-peter martin, project manager at metabo. "mrm² was the perfect partner for such a special solution."
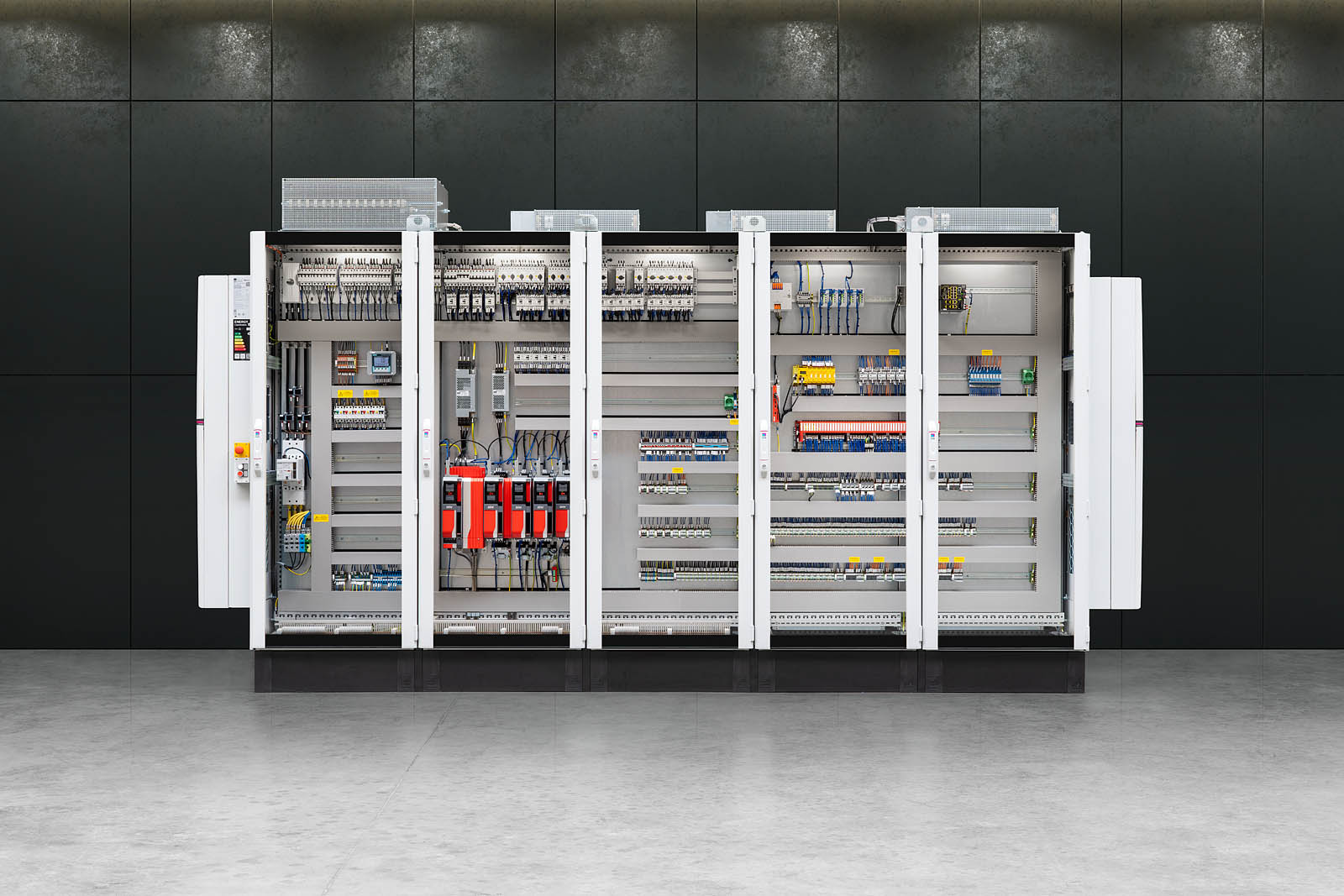
sew eurodrive gmbh
for our customer sew eurodrive gmbh located in bruchsal we built a very special switch cabinet. it is a rittal vx25 system with glass doors which provides an unobstructed view of the technology. where possible, sew components were implemented..
the project's responsible at sew, tim oestrich, is excited: "tthis switch cabinet is really top notch. everything is perfectly elaboratd and clearly arranged on the inside. on the outside it's a real eye-catcher with its glass fronts. this switch cabinet is also a great reference for ourselves, because so many sew products are installed. we're looking forward to more switch cabinets and systems made by mrm² automatisierungstechnik gmbh."
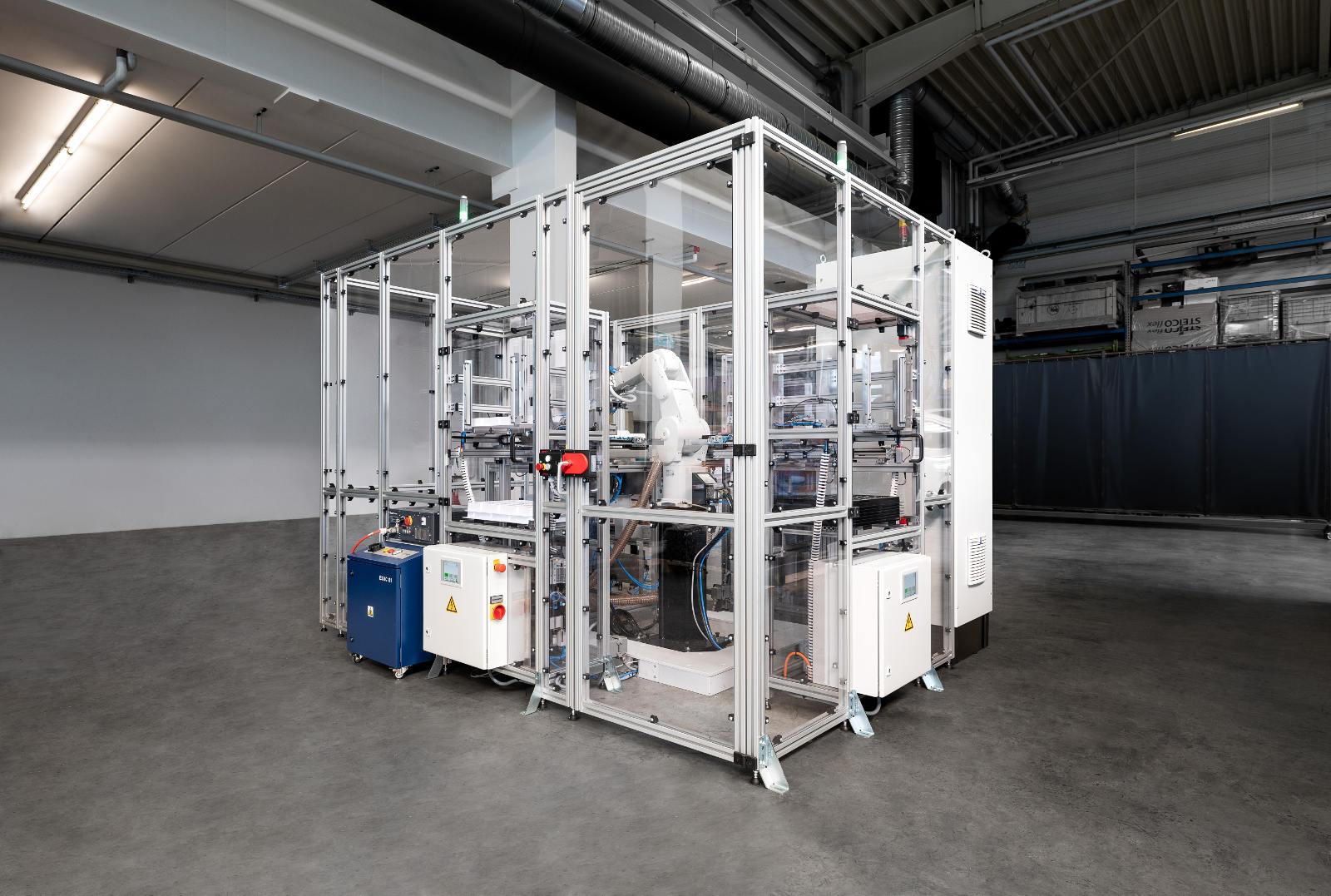
jenoptik ag
the techdax group jenoptik ag produces sophisticated optical precision systems. the precision lenses and optics to be manufactured are very complex in their production processes. ultra-precisely manufactured tools, cleanroom systems and high-precision measuring procedures are used.
the complete systems for the production of the special lenses from mrm² are characterized by perfect robot systems in combination with optimal space conditions and high-precision milling systems. they are locally processed, aligned, milled in several operations, ionized cleaned, glued, sorted and stacked. the future is virtual, and we are pleased to have been part of it.
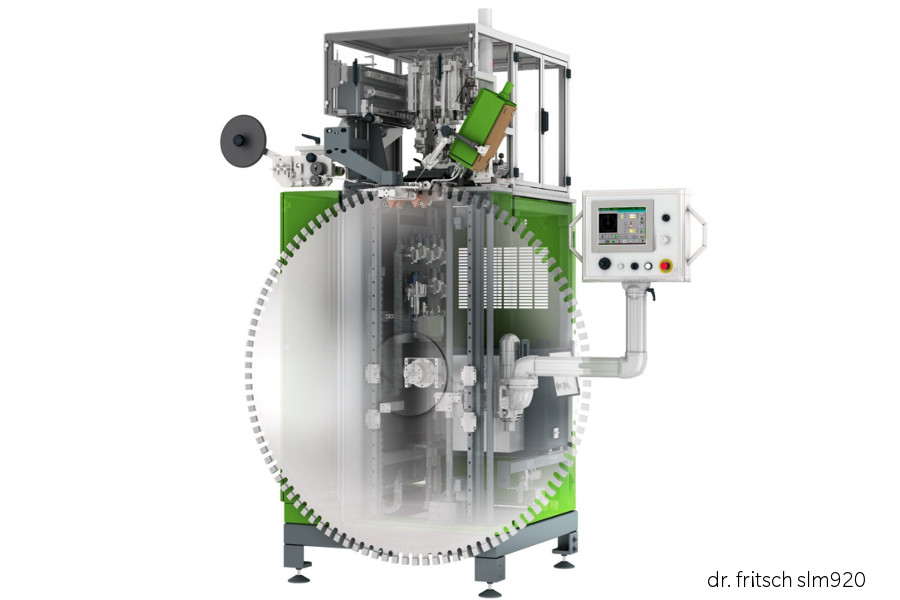
dr. fritschsondermaschinen gmbh
the special machine builder dr. fritsch sondermaschinenbau gmbh from fellbach is the market leader in the development and manufacturing of machines for the diamond tool industry. with the new machine generation slm 910 | slm 920 for automatic soldering of segments with silver solder on cutting discs, dr. fritsch made a paradigm shift. unti lnow the machines where equipped with motors, frequency converters and plc by siemens. the new machine generation should be converted to the latest technology by beckhoff and software by mrm².
with mrm² automatisierungstechnik gmbh, one of the leading specialists for beckhoff and twincat3 in baden-württemberg was selected. "after the first discussions with mrm², it was quickly clear to us: we'll do it together," says uwe funk, head of development at dr. fritsch.
our task was to replace all frequency converters and motors of the machine, and to replace the previous siemens control system with a beckhoff control system. for the control system, we developed a new, future-proof architecture and application software, as well as a contemporary visualization based on the latest standards. a particular challenge was to maintain at least a similar "look and feel" to existing plant visualizations, despite all the new features, so that users can easily get to grips with operating the plant again, despite real changes.
fully automated, diamond segments are now pressed and held onto the saw blade with a single or double gripper. the saw blade and segment are heated via an inductor, and the solder is melted. after cooling, the saw blade and segment are inseparable and perfectly soldered together.
"the close cooperation with mrm² was a big plus, as our ideas could be incorporated into the planning and implementation of the software at any time. we now have a very well planned and structured software that will make our work much easier in the future," adds uwe funk.
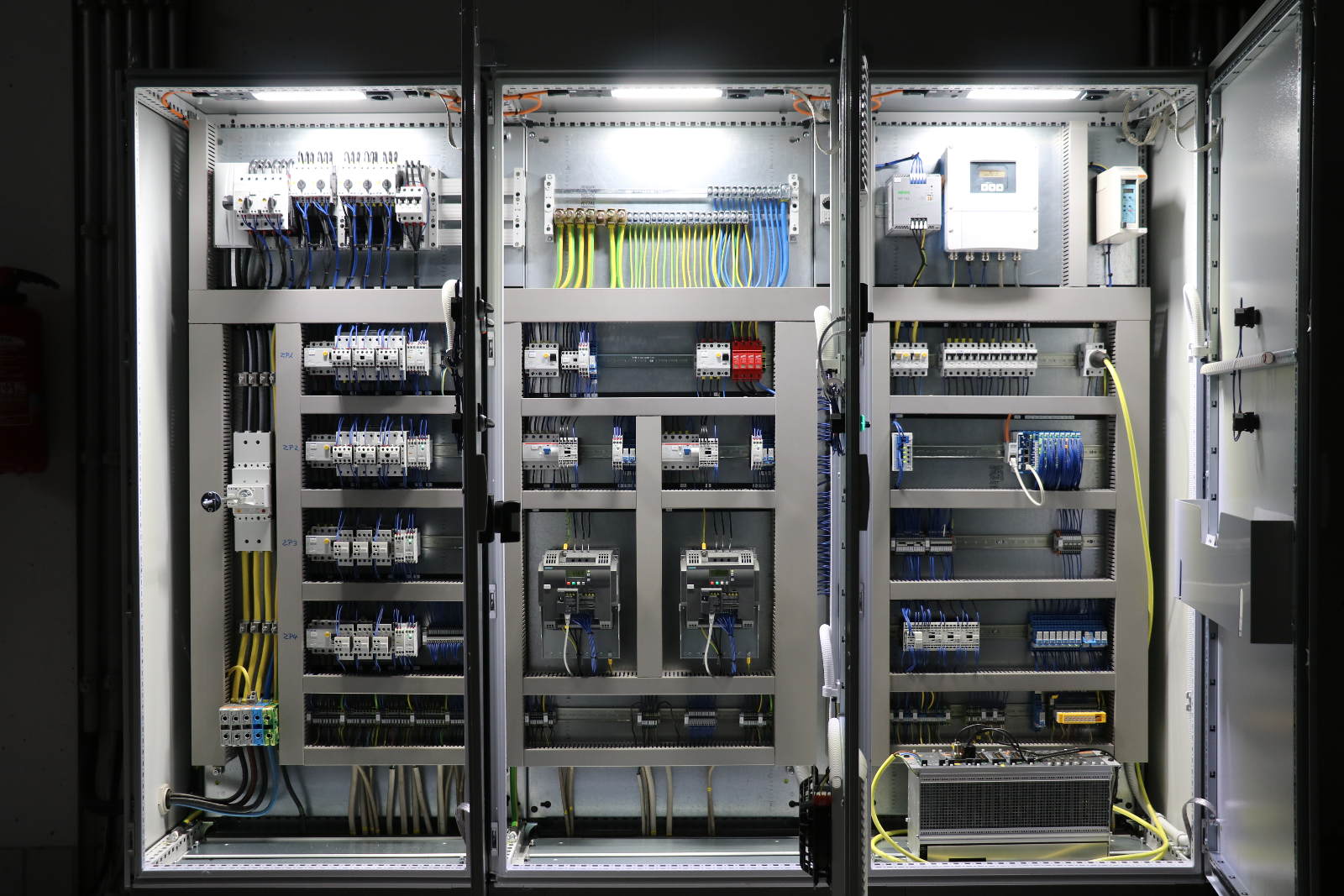
community of syrgenstein
in order to better protect our environment, water and wastewater management plays a central and very important role. in this context, electrotechnical automation is also an important component when it comes to safely executing and monitoring processes.
for the community of syrgenstein in the district of dillingen, southern germany, we carried out the retrofit of the electrical engineering of the municipal wastewater treatment plant.
old control systems for which spare parts were no longer available were successively replaced. the control cabinets were completely redesigned and equipped with the latest technology, and the installation was optimized in terms of space. the difficulty was to keep the entire plant reliably functional while individual control systems and control cabinets were gradually replaced by new ones. for example, it had to be ensured that the old communication bus was not disconnected in order to avoid error messages on the main control system that remained until the end, which would have led to disruptions in the operating process. step by step, the controls of the blower station, the agitators, the feed/return sludge and the higher-level head control were replaced. all messages now converge on a central scada system. the existing mosaic circuit diagram of the entire plant was retained in order to provide visitors with a good overview of the plant.
"the complete wastewater treatment plant is now technically up to date and equipped for many years of efficient operation!" franz seeger, responsible for the bachtal wastewater treatment plant, is delighted. "due to their many years of experience in the field of water supply and disposal and their know-how, both in dealing with the old moeller control system and the new eaton control system, mrm² was exactly the right partner for us."
would you like to know more about our projects? please feel free to contact our sales team !